How MorganHill helped a Petrochemical Company in Houston, Texas Successfully Implement ISO 9001
Background:
Our client, a well-known petrochemical company in Houston, Texas, recognized the need to enhance its operational efficiency, product quality, and customer satisfaction. They sought ISO 9001 certification to demonstrate their commitment to quality and gain a competitive edge in the industry. Facing a complex and highly regulated environment, they enlisted the expertise of MorganHill, a trusted consulting firm with a proven track record in ISO 9001 implementation.
Solution:
MorganHill began by conducting a comprehensive assessment of our client’s existing quality management practices, processes, and systems. We collaborated closely with our client’s leadership team and employees to identify areas for improvement and align them with ISO 9001 requirements. Specifically, we customized an implementation plan tailored to our client’s specific needs and goals.
MorganHill's approach involved the following key steps:
- Gap Analysis: Thoroughly evaluating our client’s existing quality management practices and documentation to identify gaps in compliance with ISO 9001 standards.
- Process Optimization: Streamlining and improving existing processes across the organization to ensure they met ISO 9001 criteria while optimizing efficiency and effectiveness.
- Documentation and Training: Assisting our client in creating the necessary quality management documentation, including policies, procedures, and work instructions. Providing training to employees at all levels to ensure a clear understanding of ISO 9001 requirements and their roles in the implementation.
- Internal Auditing: Conducting internal audits to identify any remaining areas for improvement and correct deficiencies.
- Certification Support: Collaborating with our client during the certification audit, providing guidance, and ensuring that all ISO 9001 requirements were met.
Results:
Thanks to MorganHill's expert guidance and meticulous approach, our client successfully achieved ISO 9001 certification. The implementation of ISO 9001 had several positive impacts on the company:
- Enhanced Quality: Our client experienced a noticeable improvement in the quality of their products and services, resulting in fewer defects and increased customer satisfaction.
- Operational Efficiency: Streamlined processes and improved documentation led to increased operational efficiency, reduced waste, and cost savings.
- Competitive Advantage: ISO 9001 certification strengthened our client’s position in the highly competitive petrochemical industry, attracting new clients and opportunities.
- Compliance: Our client achieved full compliance with industry regulations and standards, reducing the risk of regulatory issues and associated penalties.
- Continuous Improvement: With a solid foundation in place, our client confidently embraced a culture of continuous improvement, constantly seeking ways to enhance their quality management systems and processes.
In conclusion, MorganHill's partnership with our client resulted in a successful ISO 9001 implementation, ultimately leading to improved quality, operational efficiency, and a stronger competitive position in the petrochemical industry. This case serves as a testament to MorganHill's expertise in helping organizations achieve their quality management goals.
Talk to MorganHill today and Get the Answers You Need
Scope: We'll help you define important scoping parameters.
Documentation: We'll help you develop all required policies and procedures.
Guidance: We'll guide you through the ISO/IEC process from start to finish.
One Price: Our fees for all services are fixed.
Wherever you are in North America, Europe, Africa, or Asia, MorganHill is ready to assist.
Expertise: Since 2006, we have been an industry leader for ISO/IEC.
Knowledge: We've worked with every ISO/IEC standard currently in print.
Industry: We've worked in every major industry/sector.
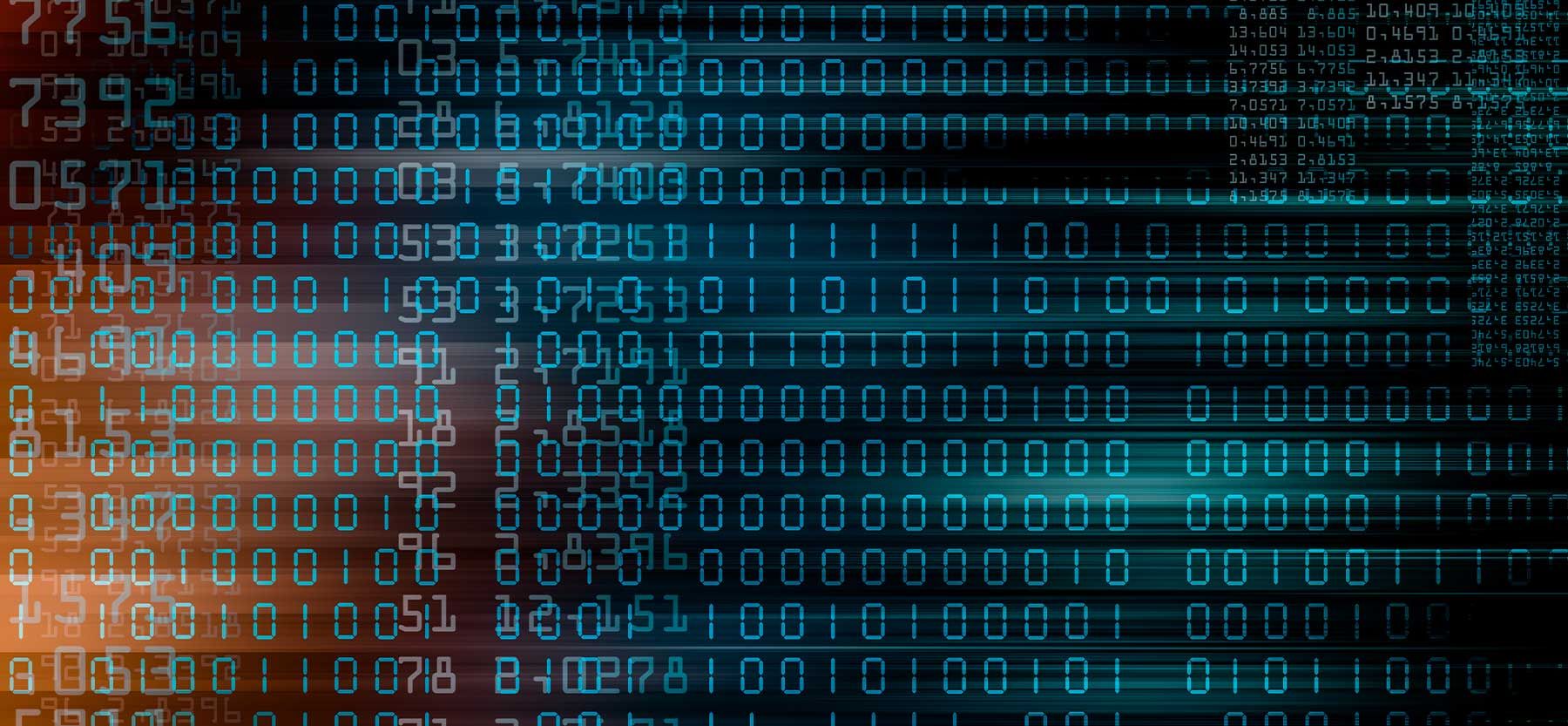
Navigating the Complexities of FBI CJIS Security Policy: How MorganHill Consulting Group, LLC Can Guide You
In an era where data security is paramount, compliance with the FBI CJIS Security Policy has become a critical necessity for organizations handling criminal justice information (CJI). The FBI Criminal Justice Information Services (CJIS) Security Policy provides stringent guidelines to protect sensitive information and maintain the integrity of criminal justice operations. At MorganHill Consulting Group, LLC, we specialize in navigating these complexities, offering comprehensive consulting and advisory services to ensure your organization achieves and maintains compliance.
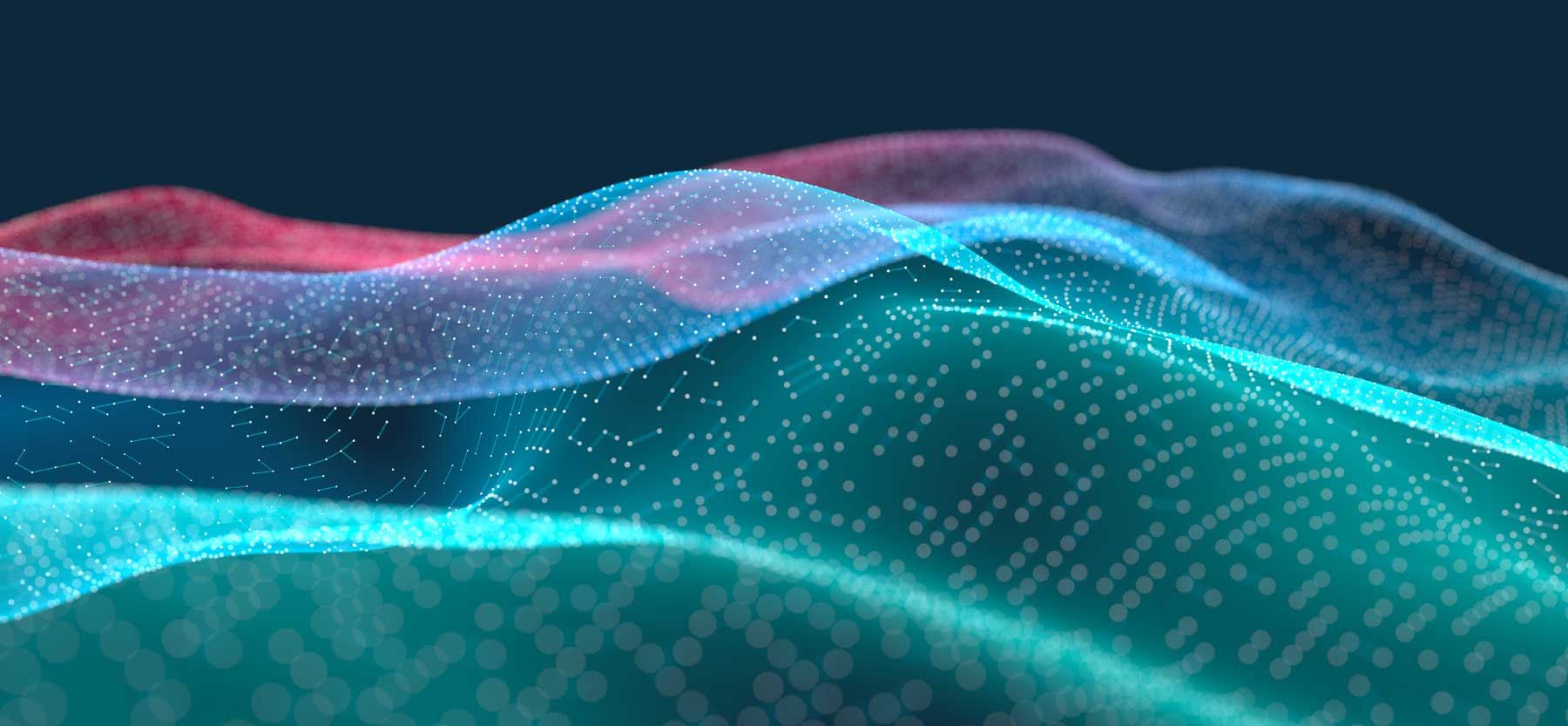
ISO/IEC 27002:2022 | 5.9 - Inventory of Information and Other Associated Assets
Per ISO/IEC 27002:20222 | 5.9 - Information Security in Project Management, “The organization should identify its information and other associated assets and determine their importance in terms of information security. Documentation should be maintained in dedicated or existing inventories as appropriate.”
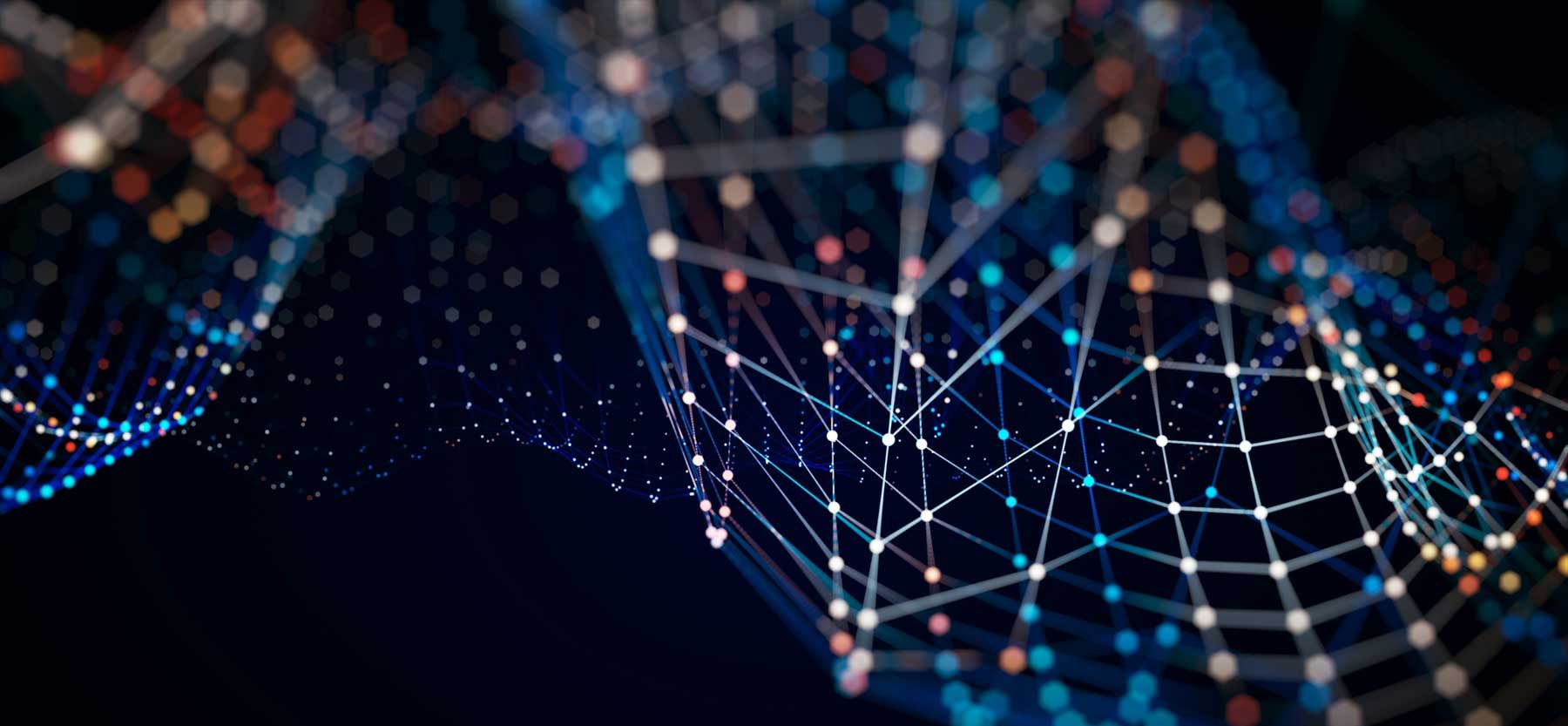
ISO/IEC 27002:2022 | 5.12 - 5.13 - Classification & Labelling of Information
Per ISO/IEC 27002:20222 | 5.12 - Classification of Information, “Information should be classified according to the information security needs of the organization based on confidentiality, integrity, availability and relevant interested party requirements. Additionally, per ISO/IEC 27002:2022 - Labelling of Information, “An appropriate set of procedures for information labelling should be developed and implemented in accordance with the information classification scheme adopted by the organization.”
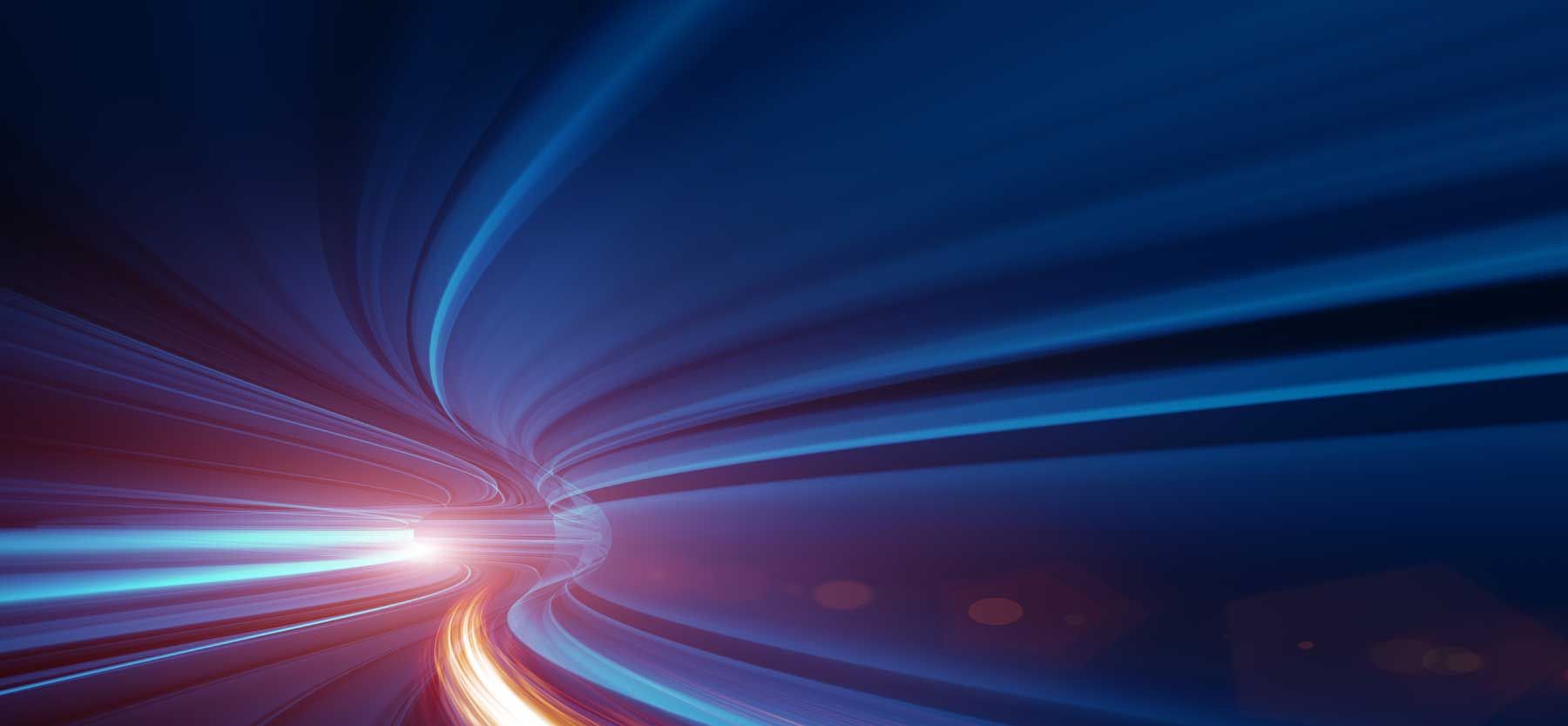
ISO/IEC 27002:2022 | 5.10 - Acceptable Use of Information | Email Usage Policy
Per ISO/IEC 27002:20222 | 5.10 - Acceptable Use of Information and Other Associated Assets “Personnel and external party users using or having access to the organization’s information and other associated assets should be made aware of the information security requirements for protecting and handling the organization’s information and other associated assets.”