QMS CONTINUAL IMPROVEMENT
ISO 9001 QMS CONTINUAL IMPROVEMENT SOLUTIONS
ISO 9001 QMS Continual Improvement Solutions
MorganHill helps organizations implement actionable, results-driven continual improvement measures as required by ISO 9001. An organization’s Quality Management System (EMS) can be challenging to monitor and continuously improve upon, regardless, it’s a strict requirement for ISO 9001, and ultimately, it makes for a better organization in many ways. As with many of the ISO standards, the concept of continual improvement - and its implementation - is left largely to the organization itself. With MorganHill, we take an often misunderstood concept and put it into action for you - the right way.
Start with PDCA for Continual Improvement
The best avenue for developing continual improvement measures is adopting the Plan-Do-Check-Act (PDCA).
- Plan: establish environmental objectives and processes necessary to deliver results in accordance with the organization’s environmental policy.
- Do: implement the processes as planned.
- Check: monitor and measure processes against the environmental policy, including its commitments, environmental objectives and operating criteria, and report the results.
- Act: take actions to continually improve.
Industry Leading Continual Improvement Strategies
Examples of real-world measures that MorganHill has assisted organization with in terms of meeting the requirements of ISO 9001 Section 10.3 for continual improvement:
- Customer Feedback Analysis: Regularly gather and analyze customer feedback, complaints, and suggestions, then using this feedback to identify areas for improvement in products, services, and customer satisfaction.
- Process Optimization: Analyze key business processes to identify inefficiencies or bottlenecks and implement process improvements, streamline workflows, and eliminate waste.
- Employee Training and Skill Development: Provide ongoing training to employees to enhance their skills and knowledge by investing in training programs that align with the organization's quality objectives.
- Root Cause Analysis: When quality issues or nonconformities occur, conduct thorough root cause analysis, thereby addressing the underlying causes to prevent recurrence and improve process reliability.
- Supplier Collaboration: Work closely with suppliers to establish clear quality requirements and expectations and collaborate on continuous improvement initiatives to enhance the quality of supplied materials or components.
- Data-Driven Decision Making: Collect and analyze data related to quality metrics and performance and use such data to make informed decisions and identify areas for improvement.
- Regular Management Reviews: Conduct periodic management reviews of the quality management system to ultimately assess the effectiveness of quality objectives, identify areas for improvement, and set new goals.
- Risk-Based Thinking: Implement risk assessment and management to proactively address potential quality issues to allow for the prioritizing of actions based on the severity of risks and their potential impact on quality.
- Continuous Training on Quality Management System: Ensure that all employees are well-informed about the ISO 9001 standard and its requirements by conducting regular training sessions to reinforce the importance of quality management.
- Benchmarking: Compare your company's quality performance to industry benchmarks and best practices, thereby identifying areas where your organization can improve to meet or exceed industry standards.
- Innovation and Technology Adoption: Stay updated with emerging technologies and innovations that can improve product quality and efficiency by exploring how new technologies can be integrated to enhance your processes.
- Internal Audits: Regularly conduct internal audits to assess compliance with ISO 9001 requirements by identifying areas for improvement and take corrective actions as needed.
- Supplier Performance Evaluation: Establish a system for evaluating supplier performance based on quality, delivery, and reliability by collaborating with suppliers to improve their performance over time.
- Feedback Channels for Employees: Encourage employees to provide suggestions and feedback on quality-related matters.
- Regularly Update Documentation: Keep quality-related documents, procedures, and manuals up to date Ensure that employees have access to accurate and current information.
Additional services offered for ISO 9001 include scoping & gap assessments, performing remediation functions, along with internal audit measures. MorganHill also offers industry leading services for ISO 27001, 22301, 27701, 14001, and 45001.
Additionally, we offer a wide range of regulatory compliance services, along with other specialty services. Furthermore, we offer world-class ISMS security documentation and other specialty documents for today’s growing cybersecurity and data privacy reporting requirements
WORLD CLASS ISMS SECURITY DOCUMENTS
Related Services
Latest Blog Posts
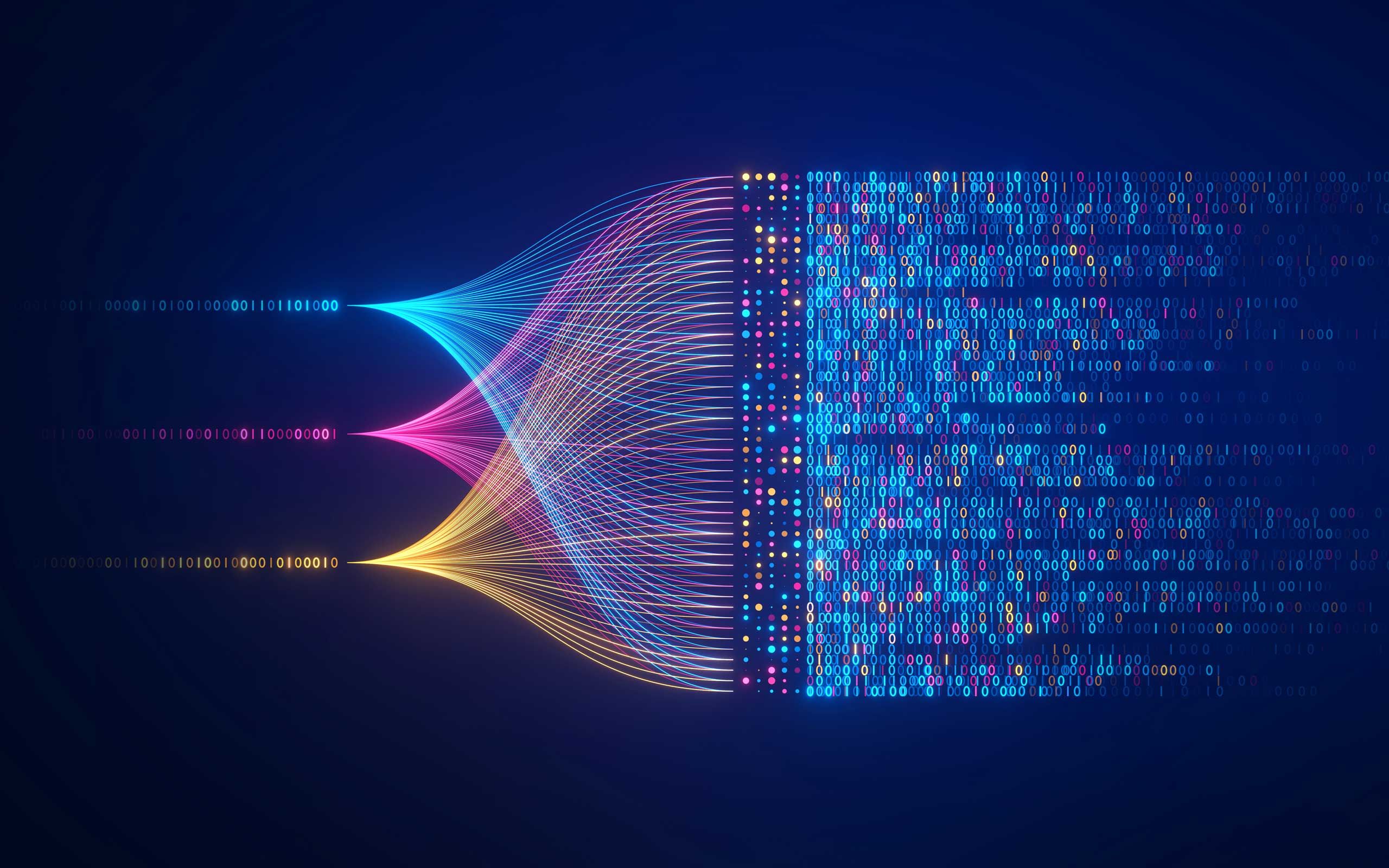
Health Technology Case Study
Four months after completing all necessary pre-certification work, the organization obtained ISO/IEC 27001 certification from an accredited ISO ANAB body that we recommend to them.
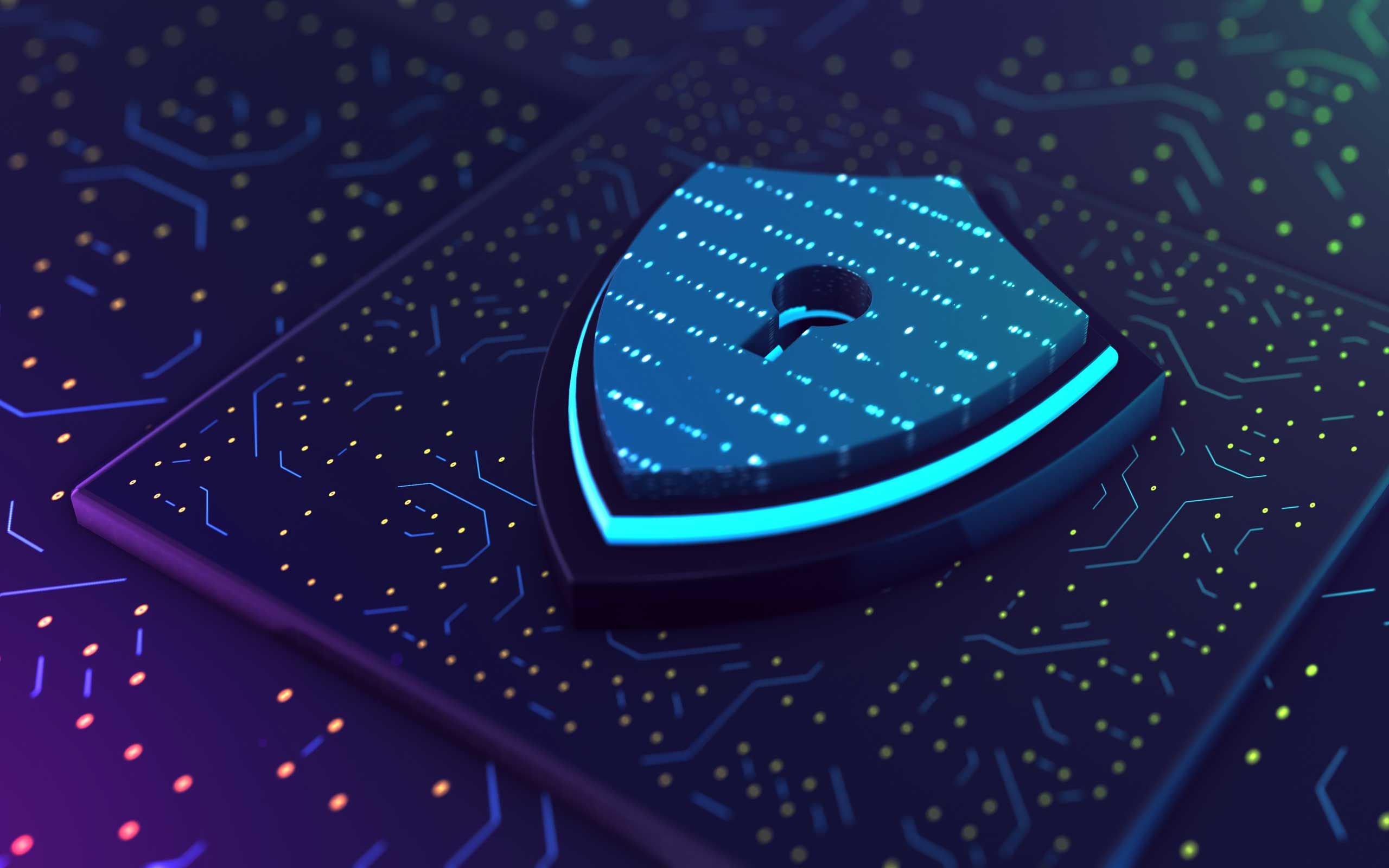
Cybersecurity Case Study
Obtained ISO 27001 certification from an accredited ISO ANAB body that I recommend to them.
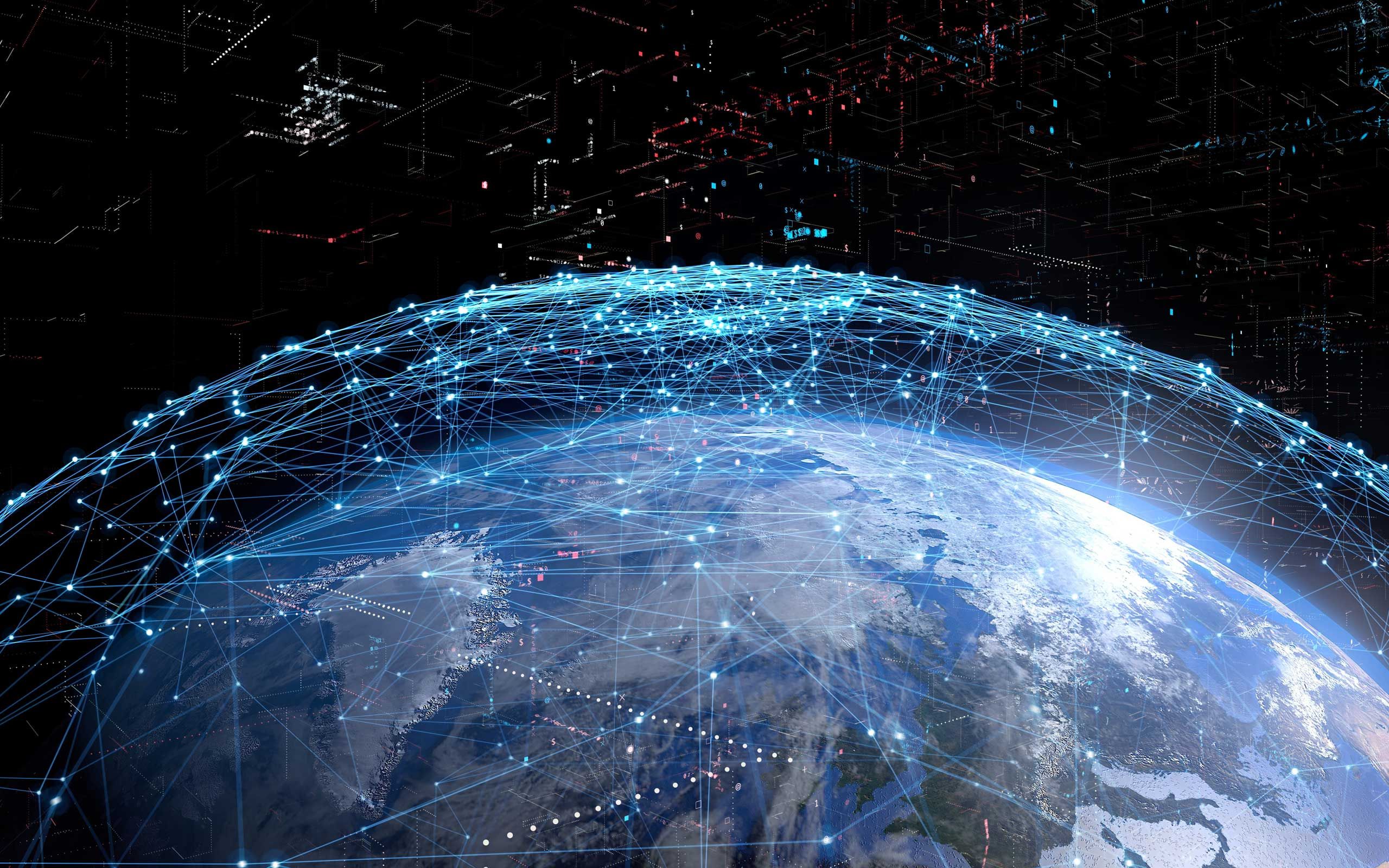
Manufacturing Case Study
Four months after completing all necessary pre-certification work, the organization obtained ISO 27001 certification from an accredited ISO ANAB body that we recommend to them.
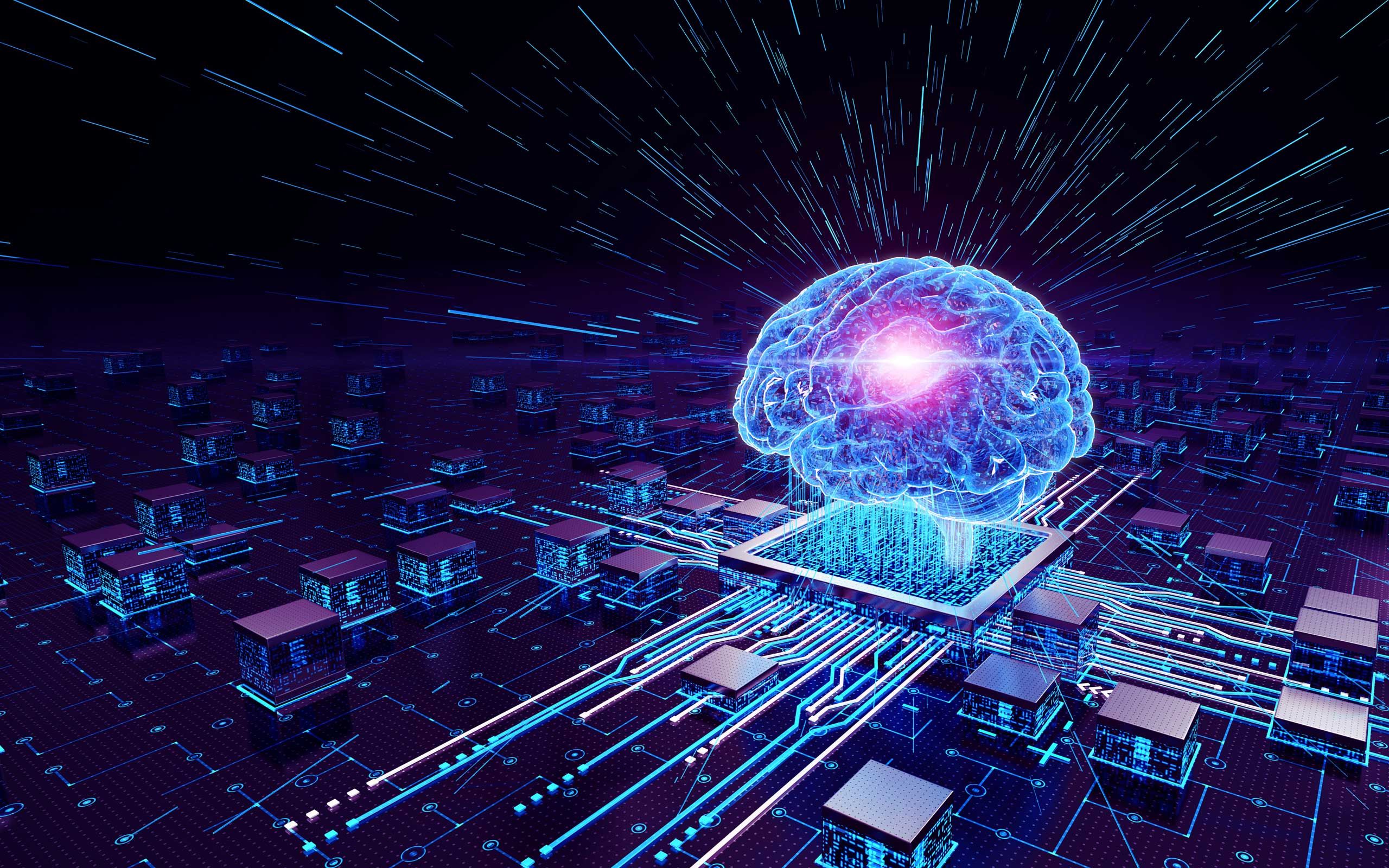
Healthcare Case Study
Three months after completing all necessary pre-certification work, the organization obtained ISO/IEC 27001 certification from an accredited ISO ANAB body that we recommend to them.
Talk to MorganHill today and Get the Answers You Need
Scope: We'll help you define important scoping parameters.
Documentation: We'll help you develop all required policies and procedures.
Guidance: We'll guide you through the ISO/IEC process from start to finish.
One Price: Our fees for all services are fixed.
Wherever you are in North America, Europe, Africa, or Asia, MorganHill is ready to assist.
Expertise: Since 2006, we have been an industry leader for ISO/IEC.
Knowledge: We've worked with every ISO/IEC standard currently in print.
Industry: We've worked in every major industry/sector.
Why Morgan Hill?
Since 2006, a Global Leader in ISO/IES Advisory Solutions.
A True Footprint all around the World.
Respected. Recognized. Resourceful.